Predictive Maintenance
Fix Before It Fails.
AI-powered condition monitoring that cuts downtime and boosts equipment life.
Unexpected component failures in rail vehicles lead to service disruptions, costly repairs, and potential safety risks. Parametric’s RET3000 enables predictive maintenance by continuously monitoring system health and using AI-based analytics to detect and predict failures before they happen. The result: fewer disruptions, lower costs, and safer rail operations.
How It Works:
- Sensor-based diagnostics continuously monitor the condition of critical vehicle components
- Machine learning models analyze operational data to identify patterns that indicate impending failures
- Custom alerts and reports enable proactive maintenance scheduling and decision-making
- Edge-based processing ensures fast, local detection without relying on cloud connectivity
Key Benefits:
- Reduced Downtime – Catch issues early to prevent unexpected failures
- Optimized Maintenance – Schedule service only when needed, avoiding unnecessary inspections
- Improved Safety – Address critical faults before they become dangerous
- Lower Lifecycle Costs – Extend the lifespan of components and reduce long-term expenses
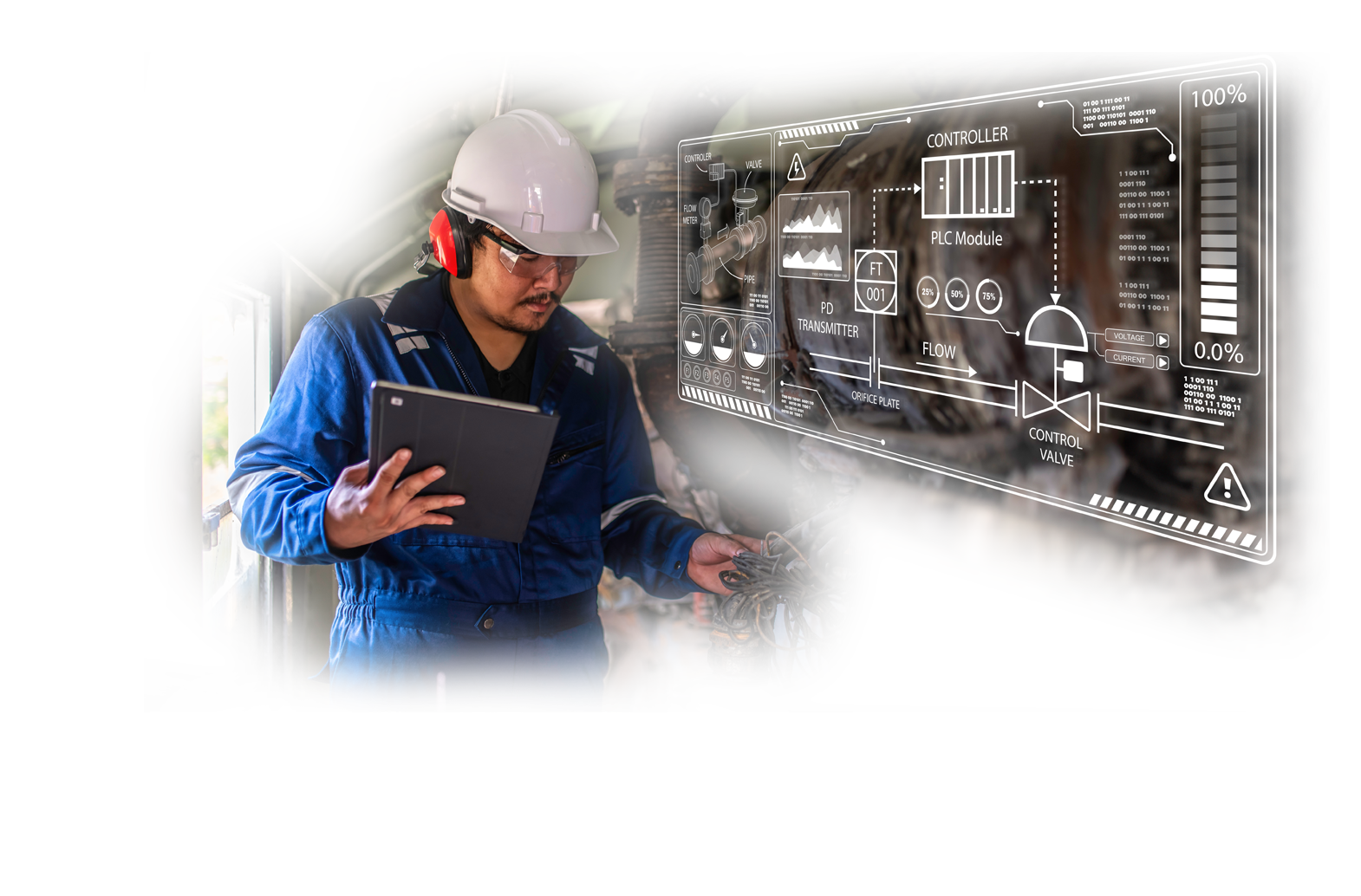
Understanding the Causes
Identifying the limitations of traditional maintenance and the benefits of predictive strategies
Successful Case Studies
Our predictive maintenance solution in action to maximize uptime and operational reliability
Intelligent Fleet Maintenance
AI-driven diagnostics and condition-based servicing for safer, more efficient rail operations
The high cost of reactive maintenance in rail operations
In traditional maintenance strategies, service is performed either at fixed intervals (preventive) or after a failure occurs (corrective). Both approaches have serious drawbacks—fixed intervals may result in unnecessary service, while unplanned breakdowns lead to costly downtime and emergency repairs.
Predictive maintenance addresses these challenges by leveraging real-time data and analytics to anticipate failures. With the right sensors and intelligent processing, railway operators can shift from reactive to proactive maintenance, minimizing risk and cost.
Key challenges solved by predictive maintenance:
- Bearings, motors, brakes, and other components degrade over time. Detecting early-stage wear avoids catastrophic failure.
Conclusion: Understanding the limitations of traditional maintenance approaches is essential for ensuring safe, efficient, and cost-effective rail operations. Reactive and time-based maintenance often lead to either unplanned failures or unnecessary servicing, both of which increase operational costs and risk. As rail vehicles and infrastructure become more complex, relying solely on manual inspections or fixed intervals is no longer sufficient. Predictive maintenance, powered by real-time data and intelligent analytics, enables operators to detect anomalies early, plan interventions proactively, and prevent failures before they occur. This shift not only improves reliability and safety but also optimizes resource use and extends the lifespan of critical components.
Challenge
Unexpected component failures in rail vehicles can lead to costly delays, unscheduled maintenance, and safety concerns. Traditional maintenance schedules often miss early warning signs, resulting in inefficient service planning and reduced fleet availability.
Solution
Parametric’s RET3000 system enables predictive maintenance through continuous condition monitoring and AI-driven diagnostics. Installed onboard, RET3000 collects real-time sensor data from critical components and uses machine learning to detect anomalies and predict failures. Local edge processing ensures fast analysis without needing cloud connectivity, while automated alerts support proactive maintenance planning.
Benefits
- Reduced Downtime: Early detection of wear and faults prevents unplanned service disruptions.
- Optimized Maintenance Perform maintenance only when necessary—no more fixed-interval checks.
- Improved Safety: LoDetect and address critical issues before they escalate into safety risks.
- Lower Lifecycle Costs: Extend equipment lifespan and reduce long-term operational expenses.
System Architecture
Integrated, intelligent, and field-ready
How our predictive maintenance solution works end-to-end
The solution is built on Parametric’s modular hardware and AI-enabled software stack. RET3000 devices are installed onboard rolling stock and continuously capture diagnostic data such as temperature, vibration, voltage, and current. This data is processed in real time using embedded ML models either locally on the RET3000 or via the RAR4000 Edge Computer.
The system generates alerts and sends summaries to cloud dashboards over LTE, giving operators full visibility into system health and enabling targeted interventions.
Components
- RET3000 Condition Monitoring Unit
Captures analog and digital sensor data from vehicle components - RAR4000 Edge Computer
Performs machine learning inference and aggregates data across multiple units - LTE Connection
Provides real-time remote access and data sync to the cloud - Sensor Interfaces
Compatible with accelerometers, temperature sensors, current clamps, and more - Maintenance Dashboard (Cloud)
Displays alerts, trends, and health scores to support decision-making - Custom Alert Engine
Defines thresholds and predictive rules tailored to each railway environment
Ready to prevent failures before they happen?
Intelligent diagnostics for reliable and efficient railway operations
With our AI-enabled monitoring devices, we provide the foundation for predictive maintenance that detects anomalies early and prevents failures. This leads to more reliable service, optimized maintenance cycles, and increased operational efficiency across your rail network.
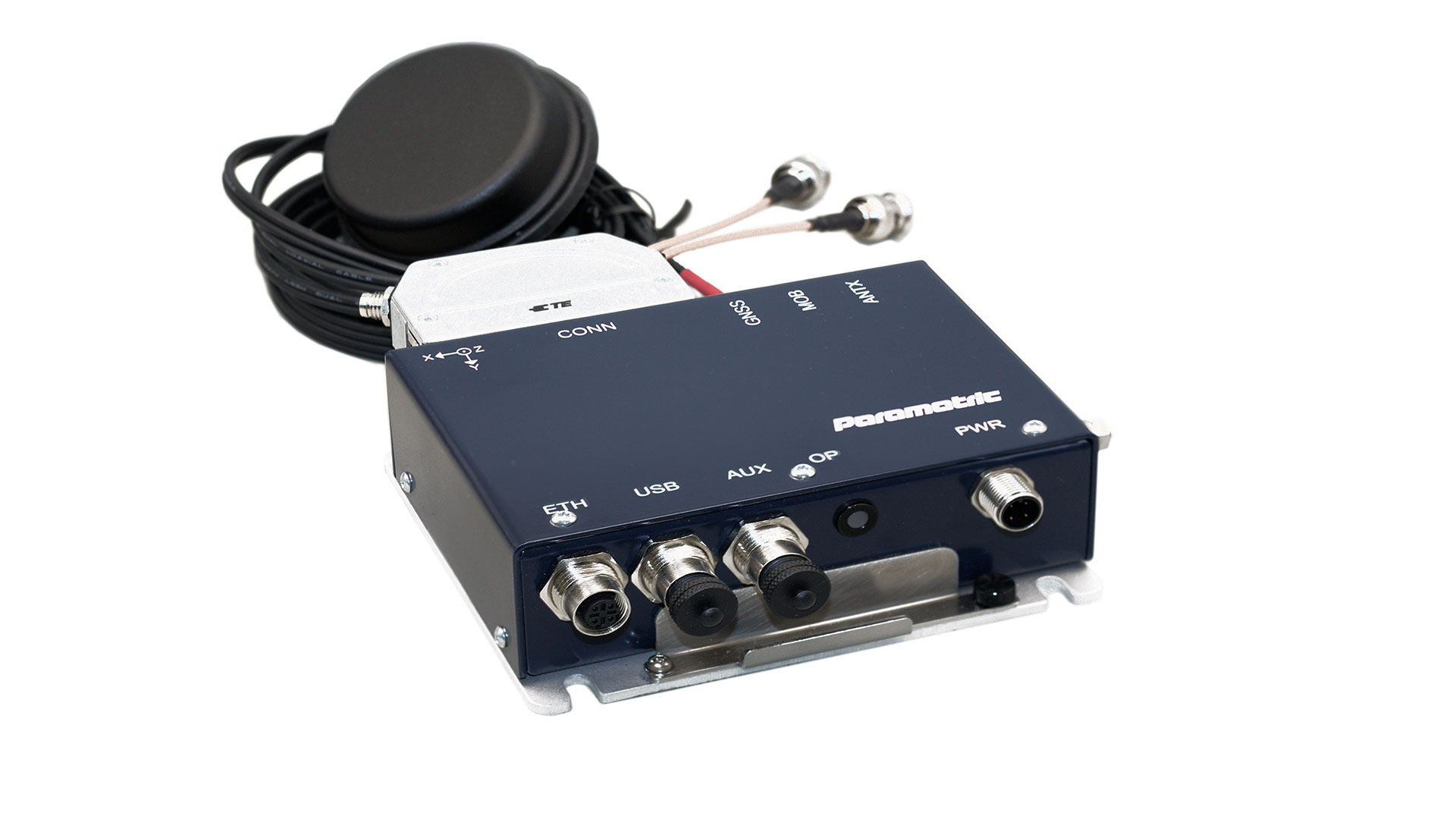
RET3000 - The Data Collector
The RET3000 Condition Monitoring Unit is part of the time-synchronized, mobile RET measurement system. It enables the acquisition of analog and digital values from external sensors.
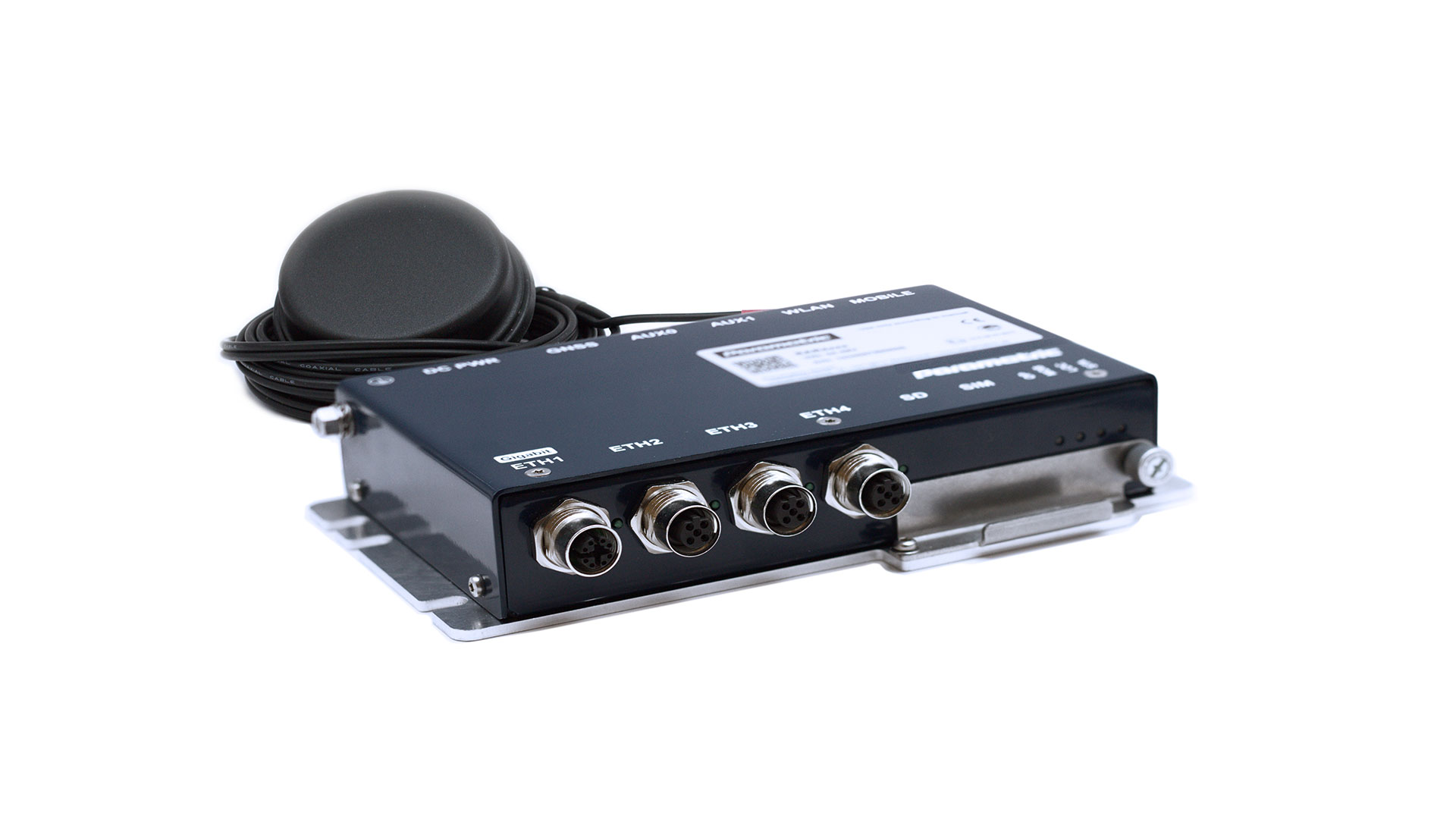
RAR4000 - The Mobile Edge Computer
RAR4000 is a mobile edge computing platform that can be used as a gateway for Ethernet, mesh or mobile, as well as for control and monitoring tasks. The hardware is designed and certified for use in trains and buses.